Line side delivery, what is it?
Let’s take the analogy of the restaurant: you are at the table, there are plates, bottles, salt, pepper and bread in front of you. You serve yourself regularly at your own pace. The waiter on his side, comes to supply the table at a lower frequency than you’re eating.
Line side delivery is the same thing: the operator “uses” pieces for assembling at his pace and the supplier comes at a lower frequency than that of the turn of keys.
Line side delivery provides the interface between those who produce, the fitters and those who transfer, internal logistics.
- The producer who assembles wants to mover as little as possible and requires the shortest workstation. It imposes compact packaging (bins or trolleys).
- The supplier wants to make his trips profitable, and requires a low delivery frequency. It imposes the autonomy of the line side and therefore its depth
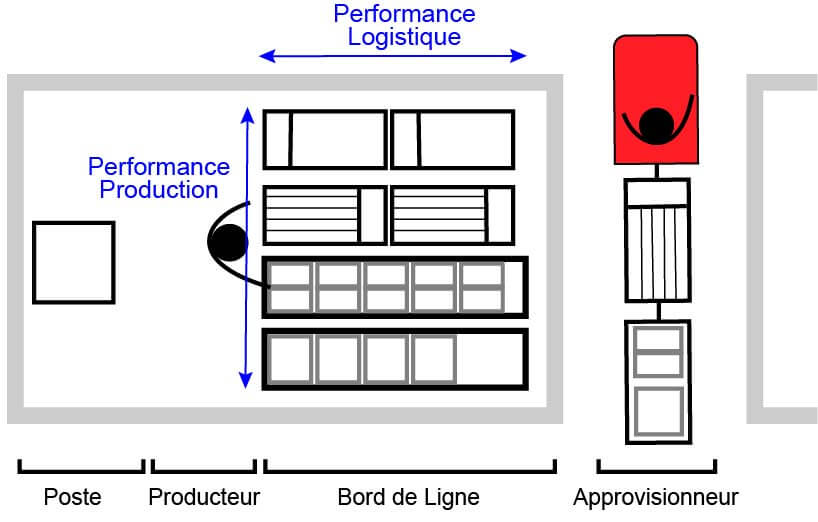
Well-designed packaging
Common ergonomic window
As it is the grip of the pieces that must be in the ergonomic window, the large pieces will be placed at the bottom. Therefore their container will be lower and the front capacity of the Rack will be increased.
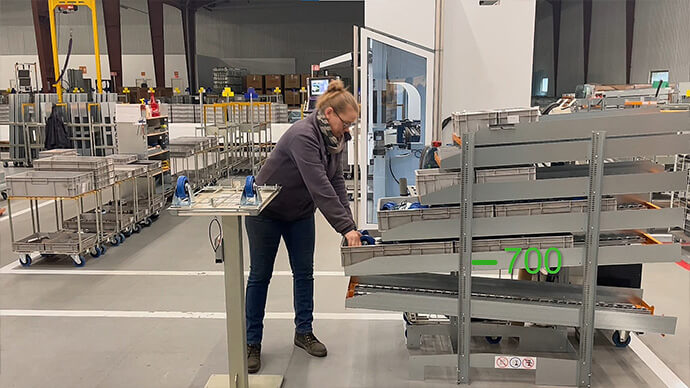
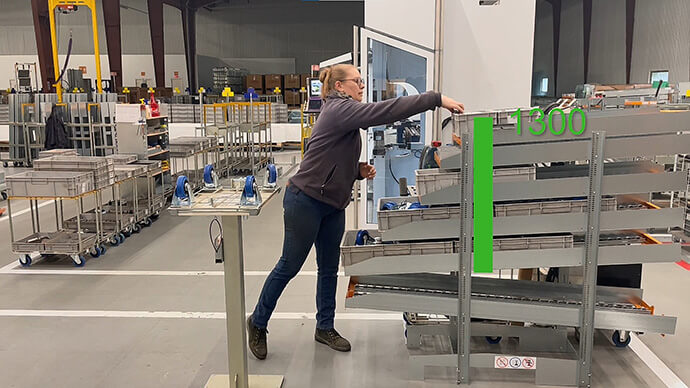
All under 1 300 mm
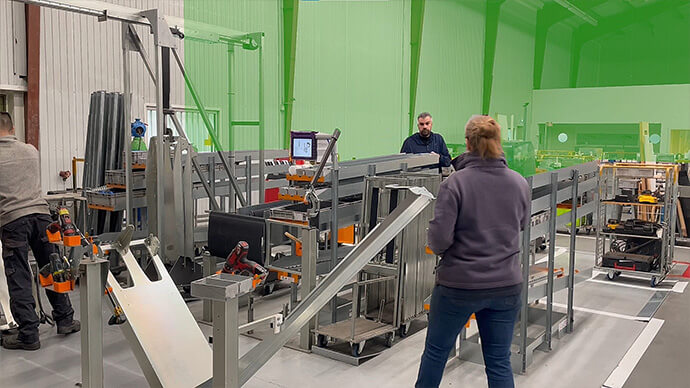
Do you need a lean solution turnkey?
A single way of supply
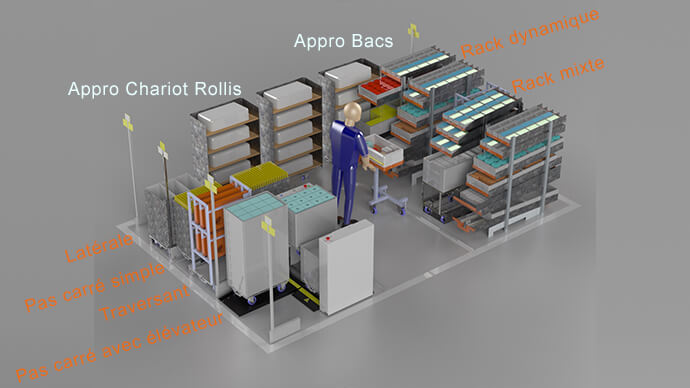
- Frontal: the pieces arrive perpendicular to the axis of the line
- Transversal: large containers or trolleys leave on the other side of the line
- Lateral: the parts are taken from the side by the operator, especially at the end of the U-shaped line
- Tangential: large pieces scroll along the sides of the line
A return line (All down the drain)
“Limit the impact of frequencies”
The return of empty containers (containers or trolleys) is perceived as a constraint for the operator whose primary action is manufacturing. By putting the return at the bottom, the operator only has to follows the container which slides naturally.
For any input check the output.
Physical guidance
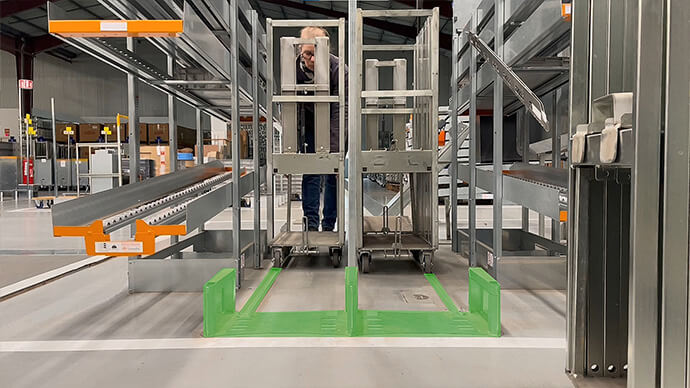
Taking from above
By using dynamic racks with taking pieces from above, the space is reduced and the number of supplied parts are increased. The surface and by the operators walk distance are reduced.
One-piece, single-layer containers
Small pieces will be placed in butter trays whose small width allows the pieces to be picked up without constraining the hand while having a small frontal surface.
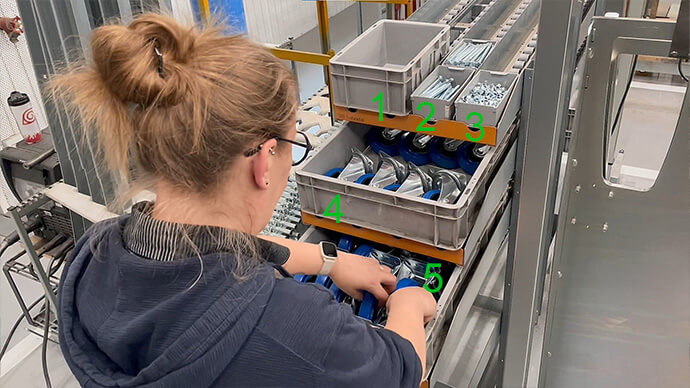
Fixed units
Straight
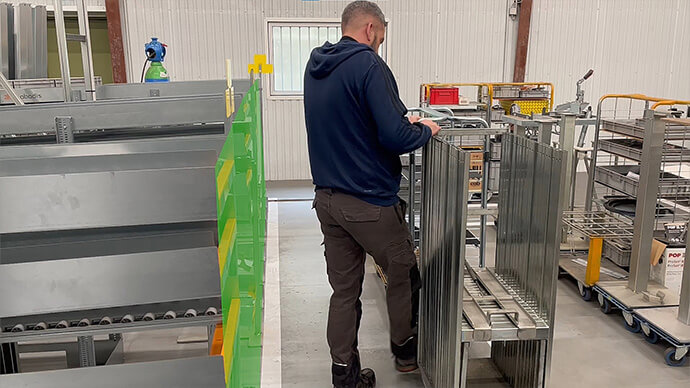
Two roll rule
A reconfigurable line edge
A gutter for the call signal
The side supply
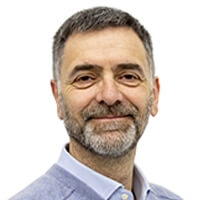